

Alternative Fuels
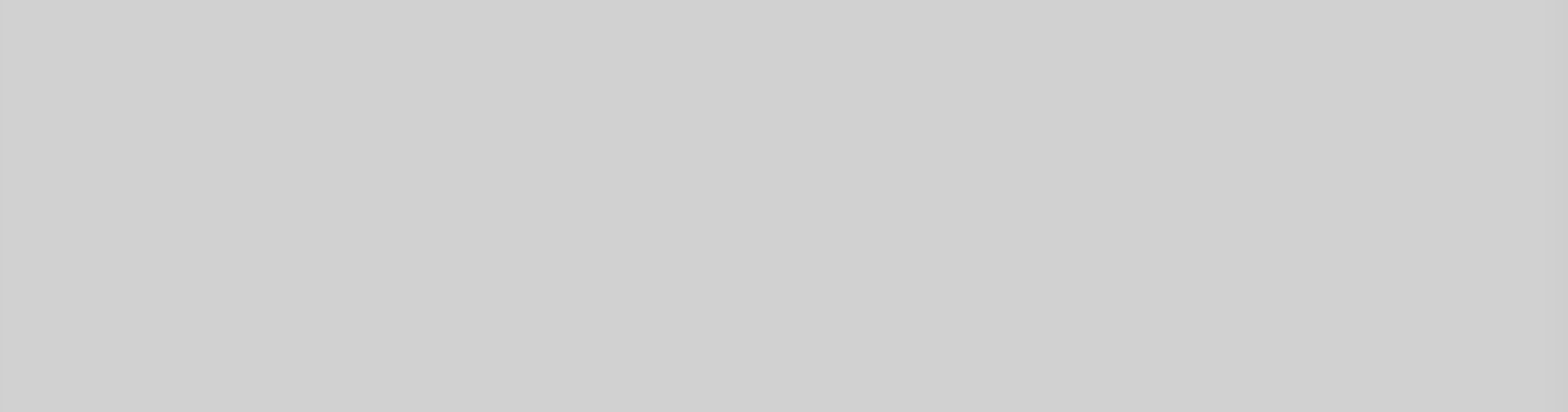

Approximately 40% of the Carbon Dioxide (CO2) generated in the production of cement clinker arises from the carbon content of the fuels used. This arises due to the traditional reliance on fossil fuels within the industry.
To address this traditional reliance on fossil fuel sources, the European cement industry has been progressively introducing Alternative Fuels (AF) for the past 30 years. This strategy has seen a significant displacement of this reliability on fossil fuel sources with approximately 20% of the energy used in firing cement kilns within the EU now accounted for by the use of lower carbon intensity alternative fuels. In many countries this practice is considered an integral component of a well managed waste management infrastructure where high recycling rates are achieved in tandem with high levels of energy recovery from residual wastes thereby reducing the dependency on landfill as a disposal option.
The many advantages of using AF in the cement manufacturing process are:
- Complete recovery of the energy value of the material due to the efficiency of the combustion process in the cement kilns.
- Reduction in CO2 emissions.
- Directly due to lower carbon emissions arising from the lower carbon intensity of the fuels.
- Indirectly by diverting material from landfill thereby reducing the potential for landfill gas production.
- Indirectly by eliminating the need for dedicated incineration capacity.
- The biomass fraction of the fuels is considered renewable and CO2 free.
- Reduction in the dependency on imported fossil fuels.
- No residual wastes are produced from the cement manufacturing process. The organic fraction contributes to the combustion process and the inorganic components are incorporated into the cement product thereby eliminating the requirement for additional landfill capacity.
- Complete destruction of the fuels due to the high temperatures, long residence times and high thermal inertia.
- Reduction in the input of raw materials and additives due to the mineral contribution from AF.
- Contribution to Ireland’s international obligations;
- Provides the most efficient energy recovery option.
- Assists in achieving national landfill diversion targets.
- Assists in meeting national greenhouse gas reduction obligations.
Irish Cement’s carbon reduction strategy involves multi-million Euro investments in the process technology required to substitute a proportion of the fossil fuels used in our cement kilns with a range of specially prepared and appropriately permitted alternative fuels as shown below:
Our first step in implementing this strategy has now been taken with the substitution of a proportion of our coal usage at Platin Works with specially prepared Solid Recovered Fuel (SRF), the primary alternative fuel to be used by Irish Cement due to its availability and technical compatibility.
SRF is the clean dry blend of fragments of plastics, paper, cardboard and textiles which arise once recycling of waste materials through mechanical and biological treatment has been completed. This fuel is produced to defined chemical and physical standards specifically suited for the cement industry.
The use of these alternative fuels to replace a proportion of fossil fuels improves our energy security, reduces the requirement for fossil fuel imports and improves our CO2 performance. In addition, recycling of waste materials is maximized in fuel preparation thereby further assisting with the national objective of the diversion of waste from landfill.
Using Waste as Fuel
TECHNICAL DOCUMENTATION
Download certifications, advisory leaflets and other data in PDF format.